Organic electrochemistry can produce chemicals with reduced environmental harm by replacing toxic, stoichiometric oxidants and reducing agents with electricity generated from renewable energy sources. Despite the advantages of electroorganic synthesis, it is rarely used to make organic chemicals on an industrial scale. One of the reasons for this is the productivity of electrochemical processes scales with the surface area of the electrode, rather than the volume of the reactor. As a result, industrial electrochemical reactors tend to be much larger than homogeneous chemical reactors for a given rate of chemical production, and thereby require greater upfront investment. Increasing the volumetric productivity of electrochemical processes, and thus their economic benefits, has long been a central goal of electrochemical engineering.
The maximum productivity for an electrochemical reactor is determined by its mass transport-limited current, IL, which for a flow-through configuration is given by:

Here n is the number of electrons required for the reaction, F is the Faraday constant, Ar is the cross-sectional area of the porous electrode, u is the superficial velocity, C0 is the concentration of reactant at the inlet, L is the thickness of the porous electrode, km is the mass transport coefficient, and As is the specific surface area. The term inside the brackets gives the single-pass conversion. If one fixes the reactor dimensions (L, Ar), the inlet concentration C0, and the flow rate u, thenincreasing the maximum productivity depends on the kmAs of the electrode.
Flow-through electrodes such as carbon paper and carbon felts have the highest kmAs values among commercially available electrodes (see Figure 1A), and therefore offer the highest possible single-pass conversion for a mass transport-limited electrochemical process (Figure 1B). However, these and other flow-through electrodes were developed in or before the 1970s, and there has been little work devoted to understanding how to create new electrodes that offer higher productivities.
We hypothesized that reducing the diameter of the fibers in a flow-through electrode to the nanoscale could greatly increase the productivity of electrosyntheses (Figure 1C). A Cu nanowire felt, made from nanowires 45 times smaller than the 10-μm-wide fibers in carbon paper, achieved a productivity 278 times higher than carbon paper for mass transport-limited reduction of Cu ions. Higher increases in productivity were predicted for the Cu NW felt based on the mass transport-limited current, but Cu ion reduction became charge transfer-limited on the Cu NW felt at high concentrations and flow rates. In contrast, Cu ion reduction was mass transport-limited on carbon paper under all conditions. Higher volumetric productivities were obtained for the Cu NW felt by switching the reaction from Cu ion reduction to Alizarin Red S (ARS) reduction, which has a higher reaction rate constant. The Cu nanowire felt achieved a productivity 4.2 times higher than carbon paper for an electroorganic intramolecular cyclization reaction which was also limited by charge transfer kinetics. This work demonstrates that large gains in productivity can be achieved with nanostructured flow-through electrodes, but the potential gains can be limited by the charge transfer kinetics of a reaction.
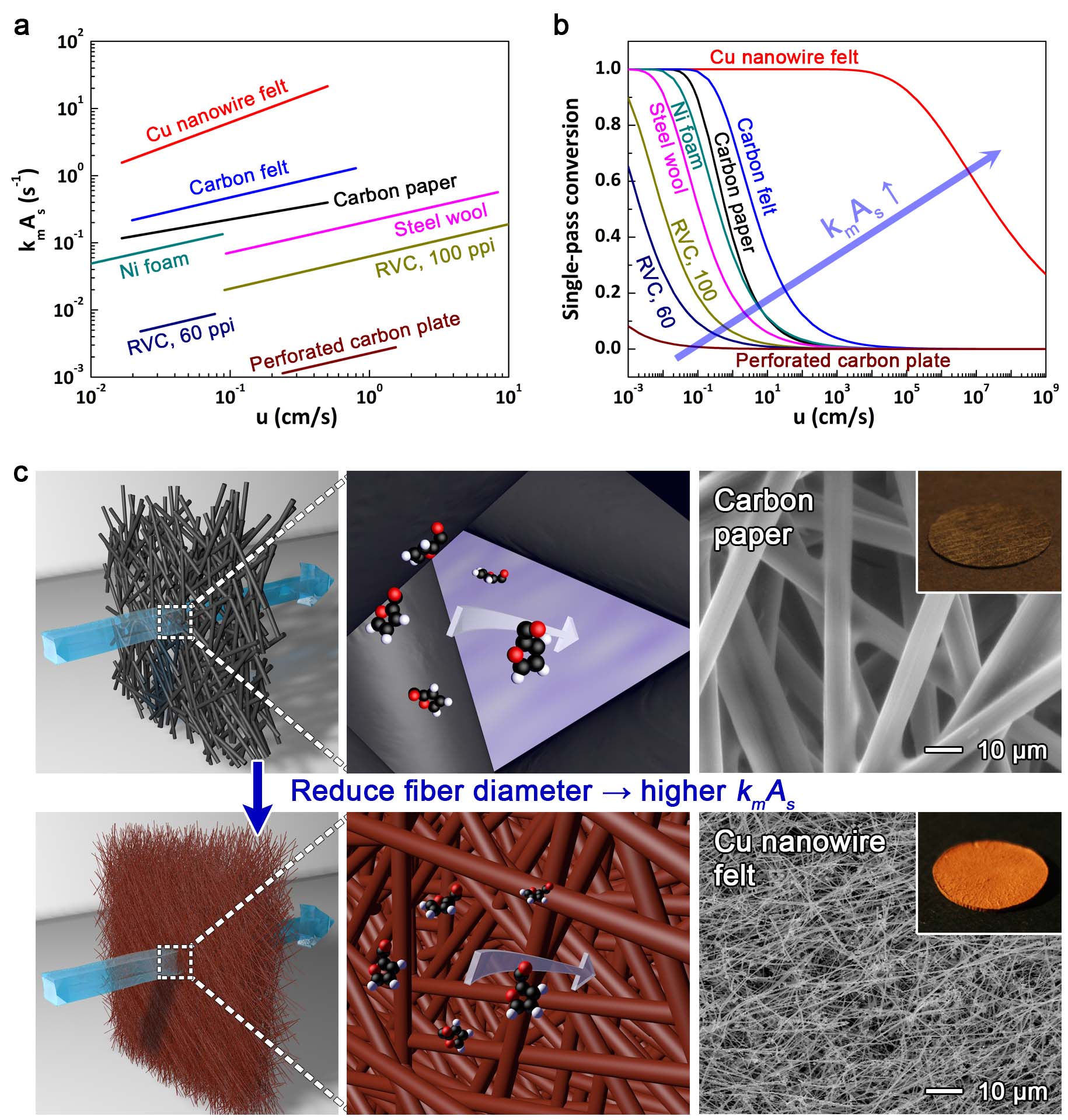
Figure 1. The performance of flow-through electrodes is determined by their specific surface area (As) and mass transport coefficient (km). (a) The empirical relationship between kmAs and u for various flow-through electrodes. (b) The associated single-pass conversion for porous electrodes that are 1-cm-thick. (c) Schematic illustration of this study’s effort to explore how reducing the size of the fibers in a flow-through electrode to the nanoscale can improve productivity. SEM images show the different diameter of the fibers in the Cu nanowire felt and carbon paper. Insets are photographs of the Cu nanowire felt and carbon paper. See the paper for more details
Related Publications:
Kim, M.J.; Cruz, M.A.; Yang, F.; Wiley, B.J. Accelerating electrochemistry with Metal Nanowires. Current Opinion in Electrochemistry, 2019, 16, 19-27.
Kim, M.J.; Seo, Y.; Cruz, M.A; Wiley, B.J. Metal Nanowire Felt as a Flow-Through Electrode for High-Productivity Electrochemistry. ACS Nano, 2019, 13, 6998-7009.