3D printing offer the promise of enabling on-demand production of highly complex and easily customizable structures while reducing material waste, energy consumption, prototyping time, and cost relative to conventional fabrication methods. However, many of the materials available for 3D printing lack the properties necessary for creating objects with the desired functionality. Achieving the full potential of 3D printing requires the development of new materials that are designed for use with this new manufacturing method. The Wiley lab has developed several new materials and methods to address the lack of functionality in commercially available 3D printing materials.
Hydrogel. To address the lack of 3D printable gels that have sufficient mechanical strength for use as tissue, we developed a shear-thinning ink formulation that enables the 3D printing of a hydrogel with a compression strength greater than cartilage. Unlike previous gels that required elevated printing temperatures (45 °C) or dissolved in water after printing, the ink we developed enabled printing at room temperature and resulted in gels that were dimensionally stable in water. Such gels present an opportunity to customize hydrogel implants, such as a synthetic meniscus (Figure 1) based on X-ray computed tomography images of a patient’s anatomy.
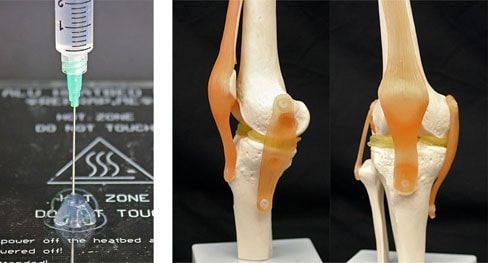
Figure 1. 3D printable hydrogel with compression strength greater than cartilage. See the paper for more details
3D Printed Electronics. Until recently, the only conductive materials that were commercially available for 3D printers were two carbon-based filaments, Black Magic 3D and Proto-pasta, which have reported volume resistivities of 0.6 ohm cm and 30 ohm cm, respectively. These low resistivities are not sufficient for these materials to be used for conductive traces. For example, a 10-cm-long, 2-mm-thick trace made from Black Magic 3D and Proto-pasta would be 150 ohm and 7,500 ohm, respectively. To address the lack of conductive materials for 3D printing, we developed and commercialized a copper-based filament, Electrifi, that has a resistivity 100 times lower (0.006 ohm cm) that previous commercially available materials (multi3dllc.com). The use of Electrifi Filament has been reported in 10 publications, including 3 led by the Wiley lab, and 3 in which we collaborated with other labs. In one example (Figure 2A), we combined 3D printed resistors, capacitors, and inductors to create a fully 3D printed high-pass filter with properties comparable to its conventional counterpart (Addit. Manuf., 2017). We collaborated with the Cummer and Smith labs in Electrical & Computer Engineering at Duke to create 3D printed microwave metamaterials (Appl. Phys. Lett., 2017) and metasurface antennas (IET Micro Antenna P., 2017), demonstrating the ability of 3D printing to create three dimensional structures with enhanced electromagnetic properties. We have combined the use of Electrifi with novel 3D printable battery materials to create the first complete lithium ion battery printed (Figure 2B) with fused filament fabrication (ACS Appl. Energy Mater. 2018). We have demonstrated that Electrifi is the only filament that enables one-step electrodeposition of copper to further improve the electrical conductivity 100-fold (Figure 2C), and improve the quality factor of 3D printed inductors 1740-fold (Addit. Manuf., 2019). These studies demonstrate the ability of our highly conductive filament to enable the use of 3D printing in a wide range of new electronic applications.
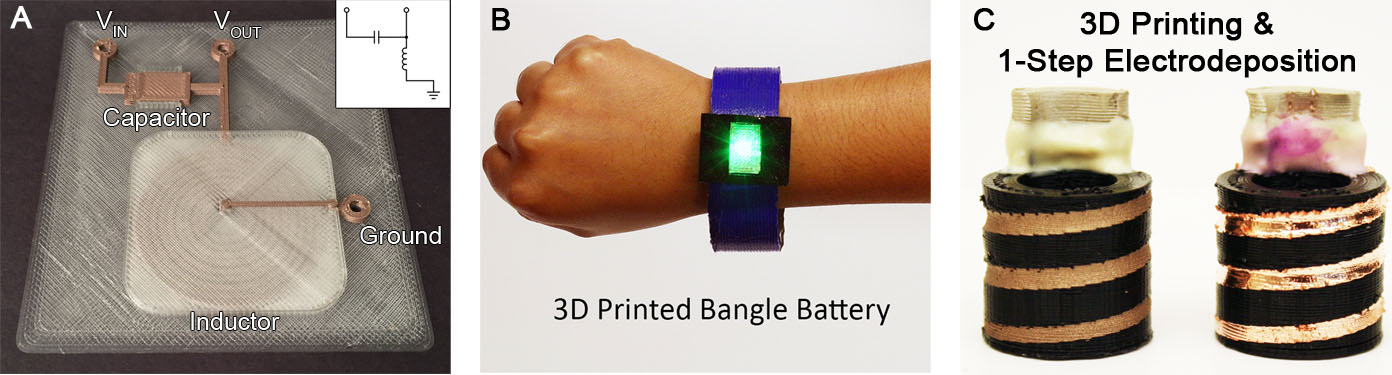
Figure 2. 3D printed Electronics. (A) High-pass filter. (B) Li-ion Battery. (C) Printed and electroplated inductor. See paper-A, paper-B, and paper-C for more details
Imaging Phantoms. We have also been working closely with Joseph Lo and Ehsan Sami in Radiology at Duke to develop novel materials and methods to enable printing of anthropomorphic physical phantoms for mammography and CT imaging. Currently available physical phantoms generally consist of simple test objects (e.g. a cylinder) embedded in a uniform region, and thus do not account for the effects of anatomical complexity on imaging performance. We developed materials to enable 3D printing of an anthropomorphic breast phantom that accurately represents breast texture, attenuation, and shape in order to enable improved detection of lesions and calcifications (J. Med. Imaging, 2019). We are also developing a low-cost, open source approach to physical phantoms for CT imaging (Proc. of SPIE, 2019, 109484Y). Figure 3 shows a preliminary example of a phantom in which we tuned the density of the printed material to mimic the contrast of a CT image of a patient’s liver. This work aims to address the unmet need for well-controlled physical phantoms with patient-like anatomy to permit task-based assessment of imaging systems that include proprietary reconstruction and post-processing algorithms.
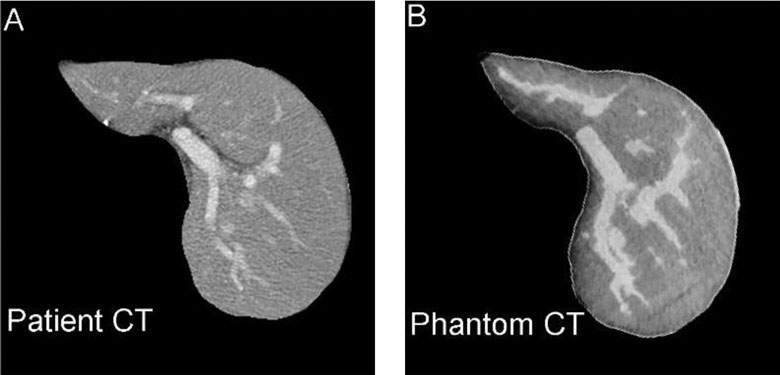
Figure 3. Comparison of a CT scan of a patient’s liver with a 3D printed phantom of the same liver. See the proceeding for more details
Related Publications:
Yang, F.; Tadepalli, V.; Wiley, B.J.; 3D Printing of a Double Network Hydrogel with a Compression Strength and Elastic Modulus Greater than those of Cartilage. ACS Biomater. Sci. Eng., 2017, 3, 863-869.
Xie, Y.; Ye, S.; Reyes, C.;, Sithikong, P.; Popa, B.-I.; Wiley, B.J.; Cummer, S.A. Microwave Metamaterials made by fused deposition 3D printing of a highly conductive copper-based filament. Appl. Phys. Lett. 2017, 110, 181903.
Flowers, P.F.; Reyes, C.;, Ye, S.; Kim, M.J.; Wiley, B.J. 3D Printing Electronic Components and Circuits with Conductive Thermoplastic Filament. Additive Manufacturing 2017, 18, 156-163.
Yurduseven, O.; Flowers, P.; Ye, S.; Marks, D. L.; Gollub, J. N.; Fromenteze, T.; Wiley, B. J.; Smith, D. R. Computational microwave imaging using 3D printed conductive polymer frequency-diverse metasurface antennas. IET Microwaves, Antennas & Propagation, 2017, 1962-1969.
Reyes, C.; Somogyi, R.; Niu, S.; Cruz, M.A.; Yang, Feichen, Catenacci, M.J.; Rhodes, C.P.; Wiley, B.J. Three-Dimensional Printing of a Complete Lithium Ion Battery with Fused Filament Fabrication. ACS Appl. Energy Mater. 2018, 5268.
Kim, M.J.; Cruz, M.A.; Ye, S.; Gray, A.L.; Smith, G.L.; Lazarus, N.; Walker, C.; Sigmarsson, H.H.; Wiley, B.J. One-step electrodeposition of copper on conductive 3D printed objects. Additive Manufacturing, 2019, 318-326.
Rossman, A.H.; Catenacci, M.; Zhao, C.; Sikaria, D.; Knudsen, J.E.; Dawes, D.; Gehm, M.E.; Samei, E.; Wiley, B.J.; Lo. J.Y. Three-Dimensionally-Printed Anthropomorphic Physical Phantom For Mammography And Digital Breast Tomosynthesis With Custom Materials, Lesions, And Uniform Quality Control Region. J. Med. Imaging, 2019, 6, 021604.
Lazarus, N.; Bedair, S.S.; Hawasli, S.H.; Kim, M.J.; Wiley, B.J.; Smith, G.L. Selective Electroplating for 3D Printed Electronics. Adv. Mater. Technol., 2019, 1900126.
Related Proceedings
Zhao, C.; Solomon, J.; Sturgeon, G. M.; Gehm, M. E; Catenacci, M.; Wiley, B. J; Samei, E.; Lo, J. Y.; Third Generation Anthropomorphic Physical Phantom for Mammography and DBT: Incorporating Voxelized 3D Printing And Uniform Chest Wall QC Region, Proc. of SPIE, 2017, 10132, 101321Y.
Rossman, A.; Catenacci, M.; Li, A. M.; Sauer, T. J.; Solomon, J.; Gehm, M. E; Wiley, B. J; Samei, E.; Lo, J. Y.; 3D Printed Anthropomorphic Physical Phantom for Mammography and DBT with High Contrast Custom Materials, Lesions and Uniform Chest Wall Region. Proc. of SPIE, 2018, 10573, 105730C.
Pegues, H.; Knudsen, J.; Tong, H.; Gehm, M. E.; Wiley, B. J; Samei, E.; Lo, Joseph Y; Using Inkjet 3D Printing to Create Contrast-Enhanced Textured Physical Phantoms for CT, Proc. of SPIE, 2019, 10948, 109484Z.
Tong, H.; Pegues, H.; Yang, F.; Samei, E.; Lo, J. Y; Wiley, B. J. Controlling the Position-Dependent Contrast of 3D Printed Physical Phantoms with a Single Material. Proc. of SPIE, 2019, 10948, 109484Y.